Why Your Drive System Needs VFD Cooling Fan
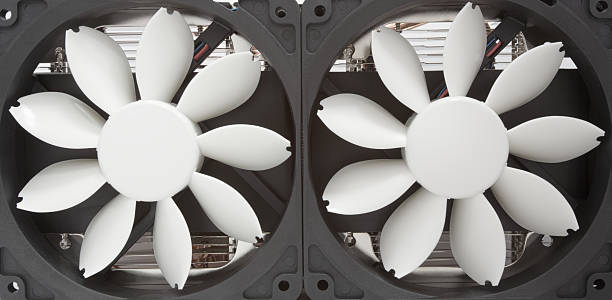
The Variable Frequency Drives (VFDs) are the core of many industrial automation systems. They control the motor speed, torque, and energy utilization. Nevertheless, their high powered electronics generate a lot of heat during operation that can degrade performance and lead to premature failure unless properly managed. A dedicated vfd cooling fan is a necessary part of any drive system as it keeps the temperature regulated even when there are variations in load. For B2B professionals sourcing thermal solutions, partnering with an oem industrial cooling fan manufacturer can make the difference between reliable operation and costly downtime.
This article delves into why VFDs need specialized cooling, how cooling fans fit into the overall thermal strategy and what to look for when selecting and integrating your drive cabinet with a vfd cooling fan. We will also discuss some of the benefits of using an oem industrial cooling fan manufacturer and installation/maintenance best practices to ensure that your system performs optimally through its lifecycle.
The Functionality of Variable Frequency Drives (VFDs) and Their Thermal Challenges
A variable frequency drive (VFD) takes the incoming AC power, converts it to DC form, then inverts it back to AC at a controlled frequency, which helps in regulating motor speed. This two-step process is achieved through the use of power diodes, insulated-gate bipolar transistors (IGBTs), capacitors and complex control electronics. Due to rapid switching of these components under load, heat is generated that must be dissipated in order to avoid:
- Thermal runaway– When overheated semiconductors enter into positive temperature coefficient regions where temperature increases cause even more heat generation.
- Component failure – Elevated temperatures reduce lifetimes for capacitors, power transistors and control boards.
- Reduced reliability – Mechanical stress from frequent temperature cycling puts strain on solder joints leading to premature breakdowns.
Inefficient heat management causes the VFD to limit current flow, fault codes or shut down completely. In high-powered or high-duty-cycle applications, traditional passive cooling such as heat sinks alone can often prove insufficient. Multiple drives, controllers and contactors may be housed together within a VFD cabinet each requiring specific airflow patterns in order to maintain safe operating temperatures. Therefore integrating a vfd cooling fan is vital towards maintaining performance levels while avoiding unanticipated maintenance costs centered around a vfd cooling fan.
In active thermal management, an active vfd cooling fan is a crucial part. To remove the excess heat which the key components generate, these fans combine forced convection with a heatsink. In practice, this process involves:
Air Induction: The Vfd Enclosure Usually has a Vented Panel or a Filtered Inlet Where Air Enters It.
Extraction of Heat: Moving air comes into contact with heatsink fins attached to control boards or power semiconductors and takes away some of their heat energy.
Air Exhaustion: In most cases, hot air is released from the cabinet through either a filtered exhaust port or an open grille at the top or rear end of its enclosure.
By doing so, the internal temperatures are maintained below critical levels leading to an efficient drive and long-life components. Different from general cooling fans that can be used for various purposes, vfd cooling fan designs suit specific airflow and static pressure requirements for drive electronics. They may contain higher RPMs, optimized blade geometries and durable bearings to endure continuous operations within industrial settings.
Additionally, uniform heat distribution and prevention of hotspots can be achieved through the use of high-quality vfd cooling fans and well-engineered heatsink combinations. For B2B integrators and OEMs, temperature control across all internal components needs to be uniform so as to facilitate predictable drive behavior and long term reliability.
Key Specifications When Selecting a VFD Cooling Fan
When appraising vfd cooling fan alternatives, engineers and procurement teams must evaluate several specifications so that they can ascertain their compatibility with the requirements of the drive as well as constraints associated with enclosure. The most critical specifications include:
- Airflow (CFM): This is an indicator of how much air can be moved by the fan which is measured in cubic feet per minute. A higher airflow is required in VFD enclosures having stacked drives or densely packed PCBs to overcome thermal resistance from multiple heat sources.
- Static Pressure (mmH₂O or Pa): Drives, filters, and ductwork cause airflow resistance. Fans with higher static pressure ratings ensure adequate airflow even through restrictive paths.
- Voltage and Current Rating: 12V, 24V, and 48V DC are some of the common industrial voltages. By selecting a fan voltage that matches your drive’s control bus or auxiliary power simplifies wiring and ensures stable operation.
- Bearing Type:
- Ball bearings have long life spans withstanding high temperatures
Sleeve bearings are cost-effective but can have shorter lifespans in high-heat environments. Fluid dynamic bearings (FDB) provide quiet operation and extended durability but may come at a premium.
Noise Level (dBA): While industrial settings often tolerate higher noise, some control rooms or enclosed cabinets require low acoustic emissions for operator comfort and compliance with local regulations.
Ingress Protection (IP) Rating: In dusty or humid conditions, an IP54 or IP65 rating helps protect the fan motor and blades from contaminants, ensuring consistent performance.
Speed Control Features: Many oem industrial cooling fan manufacturer offerings include PWM (Pulse Width Modulation) or voltage control options, enabling the fan speed to adapt to temperature changes or control signals. Variable speed operation reduces energy consumption during low-load periods.
Size and Form Factor: Fans come in square (e.g., 80×80 mm, 120×120 mm) and round (e.g., 92 mm, 125 mm) configurations. Engineers must verify that mounting holes, thickness, and airflow direction align with the VFD enclosure design.
- Lower Total Cost of Ownership: Industrial OEMs generally focus on designing for reliability and longevity. As a result, fans sourced from these companies are typically more energy efficient, have longer lives and require fewer maintenance interventions.
- Application Specific Warranty (ASW): Usually, general electronics manufacturers are unable to warranty their products based on the application. However, some OEM industrial cooling fan providers offer ASW or application specific warranties that cover failures arising solely from internal heat generation within VFDs.
- Dedicated Technical Support: Many times technical support requests of end-users using general purpose fans will be handled by sales reps who lack the required expertise to solve them. Nevertheless, partnering with an OEM industrial cooling fan manufacturer assures you of access to knowledgeable field applications engineers.
As seen in this paper, customers who source directly from popular electronics distributors find it difficult to get solutions that meet their requirements. This has led to the development of modularized design options such as VFD panel kits. The writer is not clear as to why GEICO decided this niche should be served through its own program rather than take advantage of other programs established by insurance market leaders in the country.
Compliance and Certification
Reputable OEMs ensure their fans adhere to industry standards such as CE, UL, RoHS, and sometimes ATEX for hazardous locations, reducing certification headaches for integrators.
Supply Chain Reliability
By partnering with a single oem industrial cooling fan manufacturer, businesses benefit from consistent lead times, quality control, and direct technical support—critical factors for minimizing downtime and meeting project deadlines.
Volume Pricing and Lifecycle Management
When ordering at scale, OEMs can offer better pricing tiers. They also commit to long-term availability, ensuring that replacement fans or upgrades retain compatibility with legacy systems.
These benefits make OEM partnerships especially attractive for control panel builders and system integrators who value reliability, scalability, and low total cost of ownership. Choosing a dedicated OEM provider means the fan will be engineered as part of the overall VFD solution rather than a generic add-on.
Some Recommendations for Optimal Implementation and Maintenance of the Best Vfd Cooling Fan.
Below are guidelines and practices to maximize cooling efficiency and system longevity:
- The fan should be positioned in such a way that it draws cool ambient air directly over heatsink fins or power modules. The dead zones where airflow can be restricted by cables, brackets or other components should be avoided.
- This means ensuring intake and exhaust vents are unobstructed. However, if there is the possibility for contaminants, consider removable dust filters on intakes; but keep in mind the additional pressure drop when selecting the fan’s static pressure rating.
- All wires should be carefully routed away from the airflow path of the fan. Loose cables may disrupt airflow patterns and create hotspots.
- A thermistor or temperature sensor should be connected to control logic so that as drive temperatures exceed predefined thresholds, the fan speed ramps up. This reduces fan wear during low-load periods and improves energy efficiency.
Regular Inspection and Cleaning: Nevertheless, periodic inspections should be made to the fan blades, housing, and heatsink fins in order to check their condition and dust accumulation. The cleaning can be done by compressed air or a soft brush but do not try disassembling any sealed bearing units since such has factory set tolerances and lubrication.
Bearing Lubrication Schedule: Hence whenever you are using a fan with bearings that need regular lubrication as in case of some sleeve bearing designs ensure that you follow the OEM’s recommendation for oiling intervals otherwise it may accelerate the wear.
Monitor Fan Performance: In addition, there are built-in tachometer (FG) outputs or external monitoring tools to help track RPMs and detect early signs of degradation. A decrease in speed may indicate bearing failure or blockage in airflow.
Replacement Planning: Consequently, even if one’s fans are of high quality they have finite lifespace. It would be beneficial to establish a replacement schedule based on fan MTBF (Mean Time Between Failures) ratings and environmental severity so that when failures occur, spare fans will prevent extensive downtime.
By following these implementation guidelines, B2B integrators can guarantee consistent thermal performance from their vfd cooling fan systems which will affect VFD reliability positively leading to huge system uptime gains.
Conclusion
In VFD-driven automation systems, effective thermal management is a must. A well-chosen vfd cooling fan keeps critical power electronics safe, prevents components failure before time and maintains drive efficiency. For B2B professionals, partnering with an experienced oem industrial cooling fan manufacturer ensures access to custom-engineered, high-performance fans that align with specific heat dissipation requirements and enclosure constraints.
This guide will help you optimize your VFD cabinet cooling strategy by understanding the core specifications—such as airflow, static pressure, and bearing types—and implementing best practices for installation and maintenance. Through investing in a specialized cooling solution and working with an OEM partner, one can reduce unplanned maintenance costs, prolong equipment life cycles, and achieve lower total cost of ownership for their drive systems.